Creating a Deluxe Shop Oven from an old Toaster Oven
About 6 years ago I decided that I needed a shop oven for occasionally
baking, curing, drying, or other wise heating things around the
shop. This need increased with the arrival of my first 3D printer
where I had filament to dry and desiccant to recharge. At that
time I realized that the convection toaster oven in my kitchen would be
a wonderful candidate for modifying, but if I did that, I would have to
buy a new toaster oven. Instead I went thrift store shopping and
found what has to be the ugliest home counter top oven ever made.
I rejected it at first, then realized it had everything (except good
looks) that I need for a shop oven and bought it for $5. I added
a good temperature control, rewired it and ended up with a very
serviceable unit. You can see the full story of this conversion by clicking here and scrolling to the bottom of the page.

Just for reference, here is my old shop oven.
Now to the present! (No pun intended!) I gave myself a new combination air fryer and
toaster oven for Christmas. This now freed up my old toaster
oven and I set aside for possible future modifications. A couple
weeks ago I was getting bored from a lack of a current project, so I
decided it was time to "spruce up" my old oven and create a full
feature shop oven.

This is the toaster oven I started with. Here, only the rack has been removed prior to starting work.
Design goals:
Before starting any modifications, I needed to define what I wanted in my final oven, and came up with the following:
- The size needs to be adequate for my needs. This was determined by the oven, and I deemed it to be good.
- The temperature range needs to be adjustable from room temperature to 450 degree F.
- The temperature accuracy needs to be within 5 degrees. This
was an arbitrary value I selected, but rules out a simple on-off type
controller.
- The heating elements need to be fully shielded from the items
being heated. Having a line-of-sight to a red hot element would
cause radiant heating, possibly well above the set point.
- All switches and controls must fit in the area currently used for controls.
- I desire a reliable timer if it will fit the panel area.
- Assuming a timer, I want to be able to operate in manual
mode (on as long as power is on) or through the timer with automatic
shutoff at the end of the set time.
- I want to be able to run just the fan or both the fan and heat.
- I want an indicator light that shows when power is actually
applied to the heaters, turning on and off with the temperature
controller cycles.
Work begins
I started by removing the cover which then exposed the innards of the
control compartment. There is quite a bit of room here, but there
is a fan to the left of center which could cause space problems.
Next I disconnected all the wiring to the control panel and removed the
panel. I now had access to all the areas requiring work.
After receiving the temperature controller, but not the
timer, I was able to start test fitting everything. The best I
was able to tell from the very poorly written timer specs online, was that it
was almost exactly the same size as the controller, so I used those
dimensions for trial fitting. I 3D printed a number of thin panel layouts to help judge clearances and
room for wiring. During the same time period, I generated wiring diagrams
that would satisfy my requirements. The location of the fan meant that the temperature controller and
the timer had to be at the very top and bottom of the panel. Anywhere
else would risk the unit or its wiring hitting the fan.
I was very lucky to find that I had an
industrial type panel switch that had the correct configuration of
contacts to do my primary power control. I had looked online and was
unable to find any reasonable priced units to do that. I
had most of the other parts needed. I chose to have a somewhat
complex set of switches to assure I could operate in all the modes I
wanted.

The solid state relay and its heatsink are quite large and the fan mount tab I pointed out earlier
was about the only practical location it would fit. The tab was too narrow to hold the mounting
holes so I screwed a larger plate to it and it held the heatsink.
Very baffling!
Now that I am confident that all my parts will fit, and I am still
waiting for the timer, I decided I need to get the baffles built and
installed over the heater elements. I figured that about two
inches in width should shield them adequately and still allow plenty of
airflow around them. I went on the home store websites to see
what might be available and found that 2 inch roofing drip edge would be about perfect. Home depot did not list them in
stock, but Lowes did. I bought an 8 foot length of galvanized
drip edge for under $6 and set to it with my tin snips and sheet metal
punch. Some pop-rivets and sheet metal screws, along with a lot
of time and I had my lower baffles in place. I had to attach
these to the side walls, as there is a pull-out "crumb" tray
below the elements, and it may still serve a similar service here.
The upper element is basically a square loop, with both ends passing
through to the control compartment at one of the corners. This
was much simpler! I initially cut most of the bent edge off the
drip edge prior to starting construction. I then pre-fabricated a
square of the edging,
fastening the corners with pop-rivets. The front piece was a
little longer to continue over the element ends where they went through
the wall. This piece had to be bent downward somewhat as the
elements dropped at their ends. Once the square was complete, I
attached it to the chamber top with one inch spacers.

This shows the finished heater baffles. The lower used the drip
edge intact. I cut sections from it to make the angle brackets
that mount them, and the "wings" at the end to cover the bent section.
I needed to trim most of the angle from the upper material to assure
good air flow. The right front corner is wonky (yeah, that's a
real word) where I needed to bend it down to clear the angled
ends of the element. Oh well!
I am glad that part is done! It was too cold in my shop, so I did
all that sheet metal fabrication sitting in my carpeted office, trying to keep all the little
snippets of steel under control and into the waste basket. I was
mostly, but not totally successful! I spent a lot of time with a
magnet picking up tiny circles from punched holes, tiny rectangles from the nibbler, and little
corners (I always snip a small triangular piece off every corner of
sheet metal and get a lot fewer scratches and cuts).
Back to the fun part
I had taken many measurements of the original control panel and the
mounting area for it and transferred them to a CAD drawing. I
then printed out a thin example of the shape and noted where it did not
quite fit the original curves. I made a couple minor corrections
and ended with
a very good fit. I also made several thin panels with various
mounting configurations, including one with a long rectangular slot the
right width for the two large modules. This allowed me to slide a
unit up and down, evaluating the clearance in all positions. The
results were as I first assumed; the best places for them were the very
top and bottom positions. (Thank you, fan!) I get
frustrated with the position of the fan, but without it this project
would not exist! The only way to have an even temperature
distribution is to have a properly operating fan, in other words, a
convection oven!
Once I finalized the locations of all the panel mounted
parts, I transformed it into a full thickness version with sides and
made my first actual mounting panel. I continued with this
through the full wiring process and checked out all the
functions. I found that a shortcut I took lighting the heat
indicator from the low voltage input of the solid state relay caused
the light to indicate even when the master switch was set to fan
only. Oh oh! The fix was fairly easy, and I could have just
enlarged one hole, replaced a low voltage LED with a 115 volt version
and added one wire. However there were valid reasons to reprint
the housing and rewire much of it.

Here I am test fitting all the components in the original housing. There is clearance for everything,
but cable management will be critical.
During my wiring, I thought I could get away with using the heat gun to
shrink some sleeving in the housing, after all, I used PETG which is
higher temperature than the PLA I usually use. I was wrong!
In spite of trying to use extreme care, I caused some distortion of the area around the light switch, and even
slightly distorted the name plate.
Also, I had added a wire
guide to control the exit of the wires from the panel to the
oven. This was clamped by the master switch. The plastic
washer-like addition reduced friction and allowed the switch to turn in
the panel too easily. Of course there was also the new size hole
needed for the other lamp, and really the 3 hole cluster should be
re-located slightly to better balance their positions.
So, I pulled apart the assembly I had just put together. Actually
it was almost trivial. Almost all the wires needing to be
disconnected were just clamped under a tiny plate in their specific terminal.
Loosen the screw slightly and just pull out the wire, and it could be
put back almost as easily.
This allowed me to make several changes to the control housing.
First of course was to make the heat indicator hole the larger size for
the other light. Along with that I lowered them slightly and
moved them sideways for the best visual balance. This also
required me to revise the name plate accordingly. There was no
change required for the light switch area, other than to not be
careless with this one. I also removed the wire guide that
clamped under the main switch, and duplicated it as a part of the
printed housing itself. I had actually just started printing the new
housing when I thought of one more change. The main power switch
mounts with a threaded shank just over an inch in diameter.
Around this shank are 3 shallow notches through the threads. I
revised the printed mounting hole to provide shallow tabs to fit these
notches and provide a solid keying with the switch, preventing it from
rotating at all in its hole.
The reprinted housing was totally successful and all the minor changes
added up to a large improvement. It only took a little over an
hour to re-wire it all. There were also improvements in wire
routing that became apparent examining the original version.

This is the fully re-wired second control panel. On the left
(top when installed) is the temperature PID controller, then are 3
components (switch, push button, and the new light), that are totally hidden by the
wires. Then is the master power switch and last
is the timer. The wires exiting through the new wire
channel are all the connections to the oven except for two spade lugs
from
the thermocouple (temperature sensor) which attach to two screws
on the temperature controller during installation. There are
several
wires carrying 115 volts, but only 2 connecting to the main power switch that carry the full current of the heaters.

This is the final wiring after installing the control panel.
There are 8 wires connecting the control panel to the oven in addition
to the two thermocouple
connections (red and blue lugs on the temperature controller, top
left). With the fan where it is, cable management is
crucial! To keep any wires up front
from getting to the fan blade, I printed a fan guard, barely visible in
the left picture, but shown in detail to the right. Remember when
I said the long screws
on the fan plate would be important? Well, two of them are used
to hold a plate allowing the excess thermocouple wire to be held out of
the way, and a
third to hold the fan guard.
Here is the control panel in detail:
At the very top is the chamber light switch. This was the last
control positioned on the panel and there was almost no where it would
logically fit. Finally the little corner at the top was selected.
Next is the temperature controller. It is currently showing the
default factory setting of 50 degrees Celcius. I will be changing
it to Fahrenheit. It has a range up to 2399 degrees F, so
my measly 450 degrees is no problem. Being a PID type controller,
it has excellent control of the temperature, with essentially no
overshoot when approaching the desired value.
Below
that are the mode switch, the push button and the indicator
light. The switch selects between manual mode, where the heat
will turn on immediately and stay on until you turn it off, and the
timer mode where it will turn on only for the time set on the
timer. There is a slight anomaly using the
timer. It starts its time cycle as soon as the power is turned
on, so by the time the oven is up to temperature and you might want to
start your timed cycle, the timer will be well into its cycle.
That is
the functions of the START button. Pressing this will restart the
timer. The HEAT indicator turns on whenever there is power on the
heaters. As the controller turns the
power on and off, the light will track it and turn on and off itself.
The main power switch is next. Turning it to OFF removes all
power from the oven and everything is fully off. Setting it to
FAN powers up all the instruments, turns on the fan, and allows the
chamber light to be turned on. It also starts the timer running
through its cycle. Setting it to HEAT is exactly like the FAN
setting, except that the heater is now allowed to turn on.
The final module is the timer. It has many operating modes, but
the one I will use just starts running when it gets power or when the
start button is pressed. It will then turn on the heat for the
set time which can vary between 0.1 seconds and 99 hours. I will
probably set it for 2.5 hours for most of my applications.
|
 |

The finished oven is certainly more attractive than my first one, and
more capable also. It came out better than I expected!
Oh Oh! Catastrophe Strikes? Spoiler alert: Not Really that Bad!
During the first full 250 degree F. run with the oven cover on,
I heard something briefly touching the fan blade. Checking around
the oven, the front panel metal was very hot to the touch and the
printed control panel had a slight "give" to it when I pressed on the
left edge. When I removed the cover after cooling, I found that
both the printed plate holding the thermocouple wire and the fan/wire guard
were distorted, the latter having apparently touched the running fan
blade. I was devastated! I had not run a thermal study on
the temperatures of the control section, as I trusted the Oster
engineers' design to keep it cool enough to safely run their
electronics. That should have also been cool enough to run my
electronics. Their design had plentiful vents on the top, bottom,
side and rear of the control area, and a centrally located fan, which
presumably pulled in air from the end of the oven and pushed it around
and out the top, bottom, and rear.
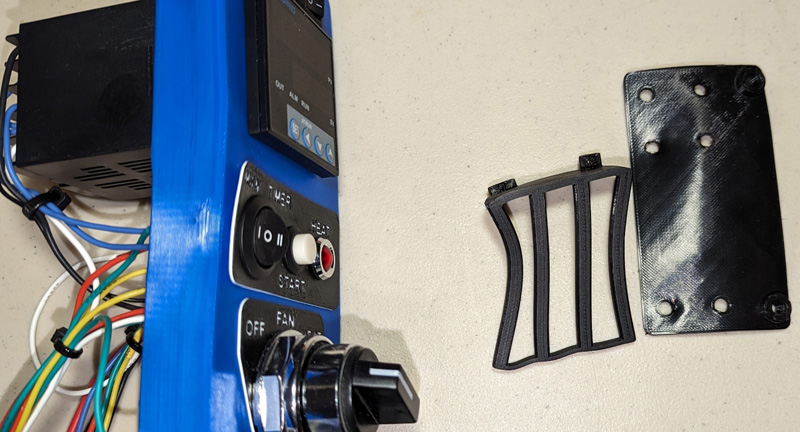
The walk of shame! Here are the parts that warped with excess temperature. The blue panel is only exposed
to particularly high temperatures on the left edge where it mounts against the stainless frame very close
to the edge of the actual oven cavity. That is where it warped slightly and even the nameplate in that area
warped. The main panel and all the nameplates are now made from ASA.
Modifications for higher temperatures:
I made 3 changes to improve the temperature resistance of the oven control area:
- I rebuilt the bracket that mounts the excess TC cable, changing from printed plastic to sheet metal.
- I fabricated a new fan/wiring shield from sheet metal and steel welding rod, replacing the printed part..
- I
reprinted the front panel and nameplates from ASA plastic instead of
PETG which added about 50 F. degrees to the softening temperature.
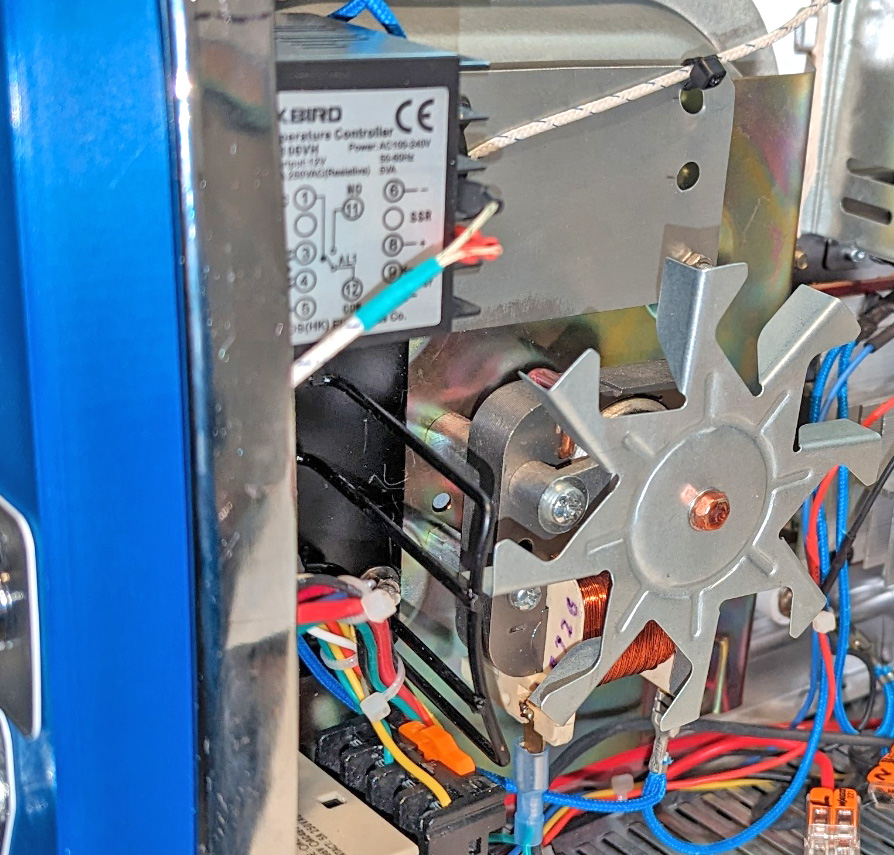
This shows the new fan/wire guard made from bent up welding rod, which was spot welded together and to a sheet metal base.
It also shows the excess wire mounting plate, the need for
which diminished a lot when I changed to a bare thermocouple and cut it to
length, meaning there is no longer a bundle. It's still handy for securing the single run of wire.
My temperature measuring equipment:
I have two pieces of quality thermocouple (TC) measuring
equipment. The first is an Omega 450 AKT hand held thermocouple
thermometer which reads out the instantaneous temperature of the TC on
an LCD display. This is the instrument I used for the control
area testing. I found this several decades ago at a yard
sale! It still works great and is still accurate!
My 2nd TC reading device is an Omega OM-EL-USB-TC thermocouple logger,
bought used from Ebay 5 or 6 years ago. It is a really cool
instrument! Removing a cap on one end of the very fat pen like
instrument exposes a male USB type A plug. The other end contains
a socket for a standard TC plug. When you plug the unit into a
Windows USB port, using their app you have 3 choices:
- Set up and start: You can
set up how often you want to take a temperature reading from every 1
second to every 12 hours, give it a file name, set alarms if desired, and
either start it immediately, or give it a date and time to start it
later. Then you unplug it and it is totally portable with an
internal battery. It can hold over 32,000 individual readings.
- Stop and download:
When you want to stop the readings, you plug it into the computer again
and hit the Stop button. Now it will stop reading and you can
save the readings to the file you selected. Once it finishes
downloading it presents a graph of the readings which you can zoom and
crop to your desires. As you move a vertical cursor line, it
reads out the exact time and temperature of any point you select.
You can then print the graph if
desired. You can also print the saved file, in readable text,
directly and receive a
full list list of the sequential reading numbers, their date and time,
and the
actual temperature readings, for every sample taken.
- View previous data: You can recall previous runs to load into the graph and do as in step 2.
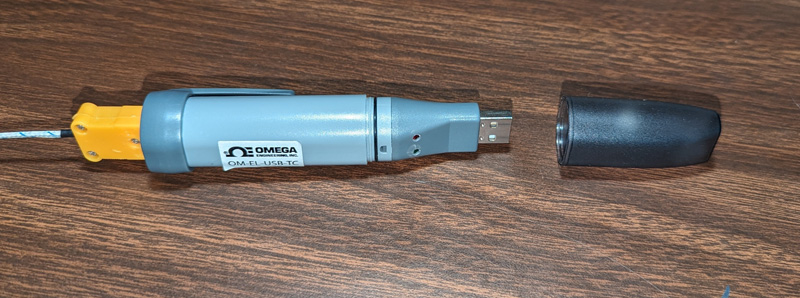
These are my two thermocouple measuring devices. The remote
thermometer is on the left, and the temperature logger on the
right. Both
are capable of reading temperatures from about -300 to +2500 degrees F. or the equivalent in degrees C.
I study the temperatures:
Now that I see there is a problem, I will do a thermal study of the
control compartment!
After a number of initial runs, placing a TC
near the temperature controller, and then adding another one clamped
between the solid state relay and its heatsink, I realized the
temperatures are not that bad! The highest I saw with the oven running at 250 F., were 126 F near
the electronics and 138 on the SSD heatsink. I decided to add an
external fan on the rear of the oven blowing in (or possibly
exhausting) in line with the heatsink. This should add additional
room temperature air to the chamber and bring it in directly through
the heatsink fins.
After adding and wiring the fan (with a temporary external switch), I
put the cover back on the oven and ran tests at 250 degrees F.,
monitoring the electronics and the heatsink. I had the following
results:
- With the fan off, the highest temperature I
saw around the electronics was 126 F. and the highest heatsink
temperature was 138 F.
- With the fan on, the electronics were mostly around 111 F. with
an occasional rise to 120 F. The highest heatsink temperature was
103.
I reversed the fan to blow out, exhausting the chamber, and if
anything, the electronics temperature rose a couple degrees. I
changed the fan back to blow into the chamber. All further tests
were with the fan on and blowing inward.
I ran tests at several temperatures, letting it stabilize at each
temperature before taking the readings. Here are those readings:
- At 250 F: Electronics - 111 F., Heatsink - 103 F.
- At 300 F: Electronics - 130 F., Heatsink - 109 F., Front metal (close to point that contacts printed panel) - 160 F.
- At 400 F. Electronics - 149 F., Heatsink - 122 F., Front metal - 187 F
I feel comfortable now running the oven at any of these
temperatures. In my design goals, I spec'd the oven to run from
room temperature to 450 degrees F., but will limit this to 400 F.
My currently planned uses top out at 250 F.
The final task was to run a number of temperature profiles using my
temperature logger to tune the PID parameters. I will not go into
the details here, but the results were mediocre by my standards,
however
almost all the results fell well within my original specs of +- 5
degrees. I am now within about +- 2 degrees. These
parameters are available to adjust on the controller at any time
without any disassembly.
Conclusions:
I started this project primarily to have a project and relieve
boredom. In spite of the initial temperature problems I had, I am really happy with the results and now have an oven
I will be proud to bring into my house if I so choose! It should
be perfect for assuring fully dry 3D printing filament and for
recharging the desiccant I use to keep it dry.
It also provided my aging brain with a couple new CAD and other
design challenges, which as my son says, saves money on puzzle books!