Miscellaneous Small 3D Printing Projects
Whenever someone finds out that I have a 3D printer, usually the first
question is "What do you make with it?" It is a simple question,
but very difficult to answer. My initial answer is sometimes
"Everything!" or "Anything I want!" two accurate, but almost useless
answers to the asker. I then try to describe several recent
projects I have done, with varying degrees of success.
For many years I have been using this website to describe a number of my more
significant projects, often ignoring the many and frequent smaller
ones. Sometimes these consist of a single small
piece, to replace something that broke, to solve a problem, or to make
something more convenient.
This chapter illustrates a number of "minor" projects I have done in 2024. It is meant as a way to
illustrate some of the typical smaller uses for my printer.
Here is a listing of the projects shown in this report. Clicking on a title will take you to that section:
Belt and Tie Holder
Filament Holder
TV Tilt Mount
Cloner Stand
Heel Lifts
Tissue Holders
Deej Mixer
Webcam Mount
Cable Holder
Water Heater Vent
Mini-screwdriver Case
CPAP Hanger
Component Tester Case
Cluttered Cord Manager
Belt and Tie Holder
These hangers for my closet, designed to hold my belts and ties are an
example of realizing a need for something, figuring out what that
something should look like, and then making it. I had never
really had a good place to store my excess belts, and I had a bulky tie
holder which not only took up way too much space, but did not hold even
my meager selection of ties.
For my ties, I decided I just wanted a place to hang them, 2 or 3 together
in a way that took very little space in my closet. I found that a
hanger device with slots for several sets of ties worked very well.
For my belts, I made several branches with sawtooth tops, which would hold
and separate my belts just fine. I rotated the bottom level to
spread the belts out a little.

For my belts I printed a two layer hanger, then dipped the bottom in boiling water to heat it and twisted it 90 degrees.
The tie holders were just printed flat.
Filament Holder
When I built my original printer, the kit came with a filament reel
holder which clipped to the top frame of the printer and held a single
reel of filament. This was fine until I built an enclosure for
the printer where I wanted the filament on the outside. To initially solve
this problem, I made a simple (non-3D printed) frame which supported a round rod to hold
the reels. To change a reel, I had to lift the rod from its
slotted supports, remove the old reel and slide the new onto the rod, then
place the rod back in its supports. If I had a couple nearly full
reels, this was heavy and somewhat awkward, but worked well for a
number of years.
When I built my latest printer at the end of last year, I tested it
outside the enclosure using the reel holder they supplied, and really
liked it. It is a double ended holder, with a cantilevered bar for
filament on each side, so there is no more lifting a rod out to load or
unload, and there is now a filament guide for each reel in the front. I did not
think much about this guide at first, but as I used it I found that it
was a MAJOR improvement, controlling the path of the filament very well. It also kept the end of the filament
from snapping back onto the reel and possibly tangling. I wanted
to retain this holder!
This holder also snapped onto the top frame of the printer, but
obviously could no longer do that with the enclosure in place. I
did not want to destroy the holder by cutting and bolting it to
something, so I designed a "frame lookalike". I printed an angle
piece with a long enough section the same size as the frame top to
mount the holder. I can now snap the holder to this piece,
bolt the angle to a base and I have my new holder.

The reel holder I have been using for years had a simple lift-out axle
which supported up to 2 reels of filament. The one which came
with my latest printer,
shown on the right, cantilevers axles to each side from a center support. It also has filament guides on the front.
To support the new holder outside my enclosure I printed a beefy angle
with a section the size of the top frame. The holder snaps on to
it, and it is
then mounted to the same base I used previously.
TV Tilt Mount
My office TV is placed on a DVD/VCR on a shelf, and is a couple feet above
my head. To view it well, it needs to be tilted forward so I can
view it head-on, otherwise the picture is washed out. For far too
long, I accomplished this by placing an old battery pack (the first
thing I found that was the right thickness) under the rear edge
of the TV base. This tilted it at a good viewing angle, but was
much too close to the tipping point of the whole TV. I finally
decided that it was time to make a proper adapter which would still tip
the TV forward, but do it in a manner that was stable and safe!

I initially picked the first thing I found that was the right
thickness, a dead RC car battery, to put under the rear of the oval TV
base to tilt it forward.
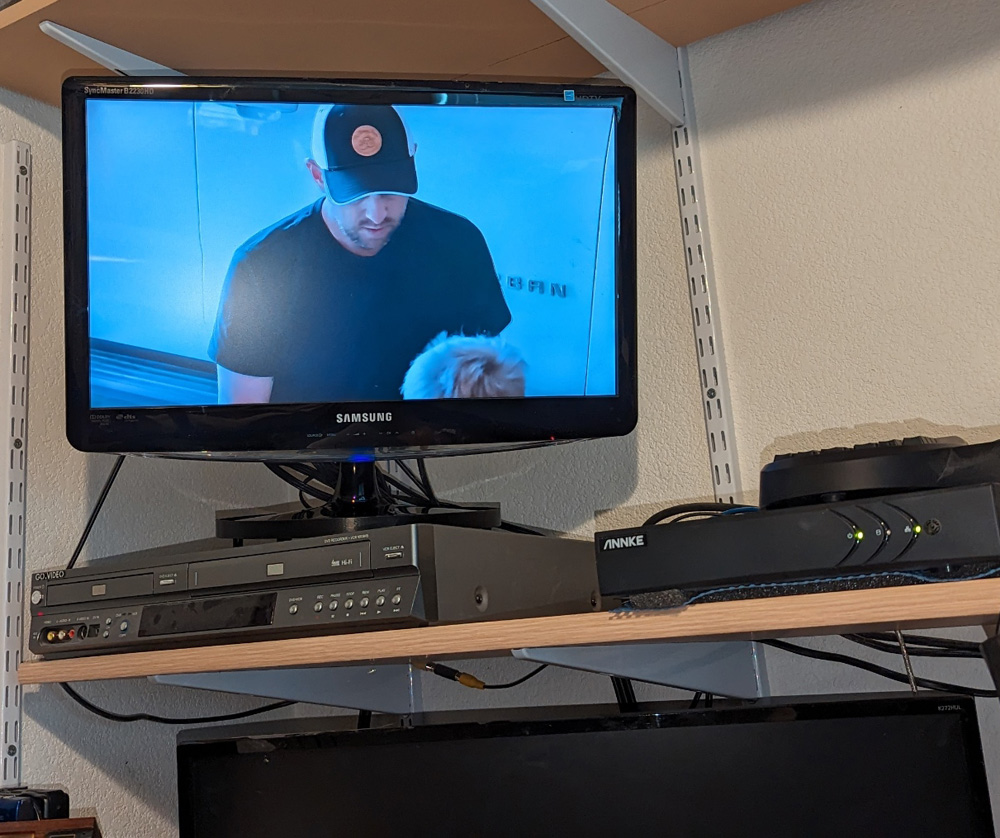
The tilting adapter I made is an oval ring to fit the TV base held at
an angle to a base ring. The top has clip on the rear
to keep the TV from tipping out of the base, and the bottom ring is extended a couple inches on the front to assure stability
and keep the entire assembly from tipping forward.
My TV now still tilts forward, but is stable and secure!
Cloner Stand
I have a marvelous device called a Cloner Alliance View Pro which is a
standalone video recorder which can accept almost any video source.
I use it quite a lot. The built in display is wonderful, except
it is at an awkward angle when place flat on a desk. I decided it
needed to be at a slight angle to be really easy to use. I
quickly designed and printed a framework which does just that.
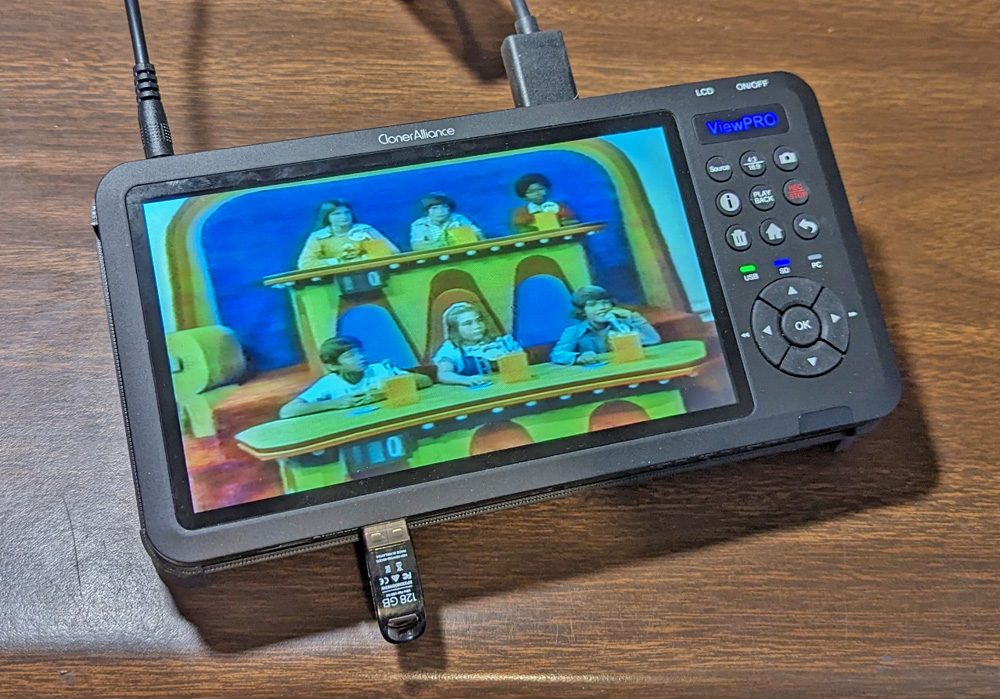
The left shows my View Pro and the frame I printed to support it at an
angle. Note: The boy in the image is my son, who is now
retired and has two married daughters!
Though hard to show in a picture, the right shows the device in its angle stand.
Heel Lifts
Whether due to nature, or a couple knee and an ankle replacement, my
left leg is somewhat longer than my right one. My orthopedic doctor
gave me a pressed cotton heel lift to put in my right shoe which
helped, but only partially. He apologized for not having a
thicker one. I thought of the idea of printing my own, but
procrastinated until a neighbor - out of the blue - asked if I could
print a couple of heel lifts for her. Her doctor had told her
what she needed, so I told her I would try. I bought a spool of
TPU, a somewhat flexible filament and printed her a pair. It took
a couple of tries before they were just right for her, but she was very
happy with them.
Then I decided it was time to print my own. I printed one and
showed my doctor. He was impressed and made a couple small
suggestions for improvements. I ended up printing two of them and
put one in each of the pairs of shoes I mostly wear. They work
great! I no longer lean to the right when I think I am straight!
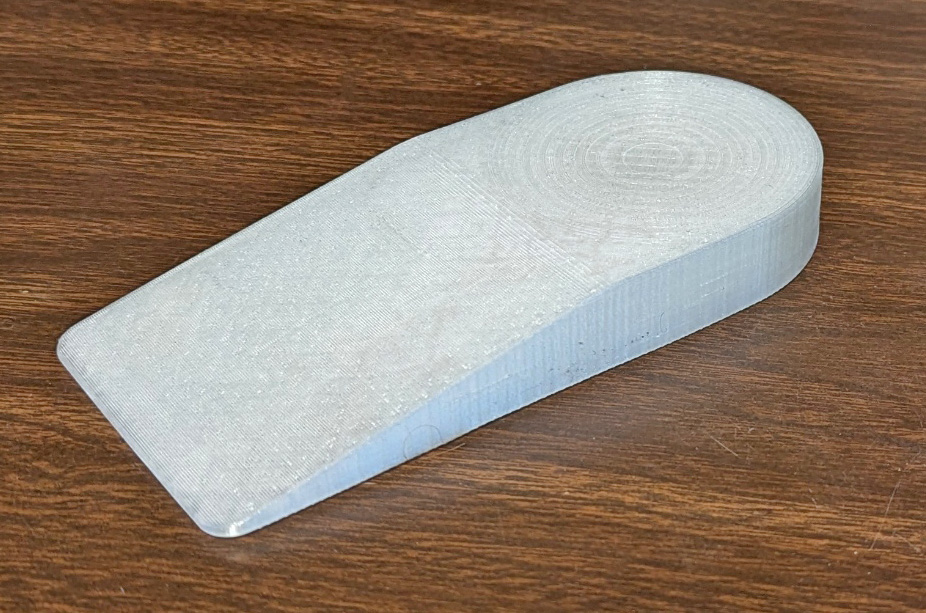
I am printing a pair of heel lifts for my friend on the left. On the right is the final version of my own heel lift.
Tissue Holders
For some time now, I have kept a box of Kleenex and a box of Kimwipes
(tougher tissues bought at auction from my former employer when they
moved the operation to the East Coast) on my side desk. These boxes have always
been a nuisance and in the way. I decided to print box holders
for the two sizes of boxes and mount them off the surface of my
desk. I first had to figure out how to print the boxes without
needing to have massive areas of support material. They came out
fine and I am well pleased.
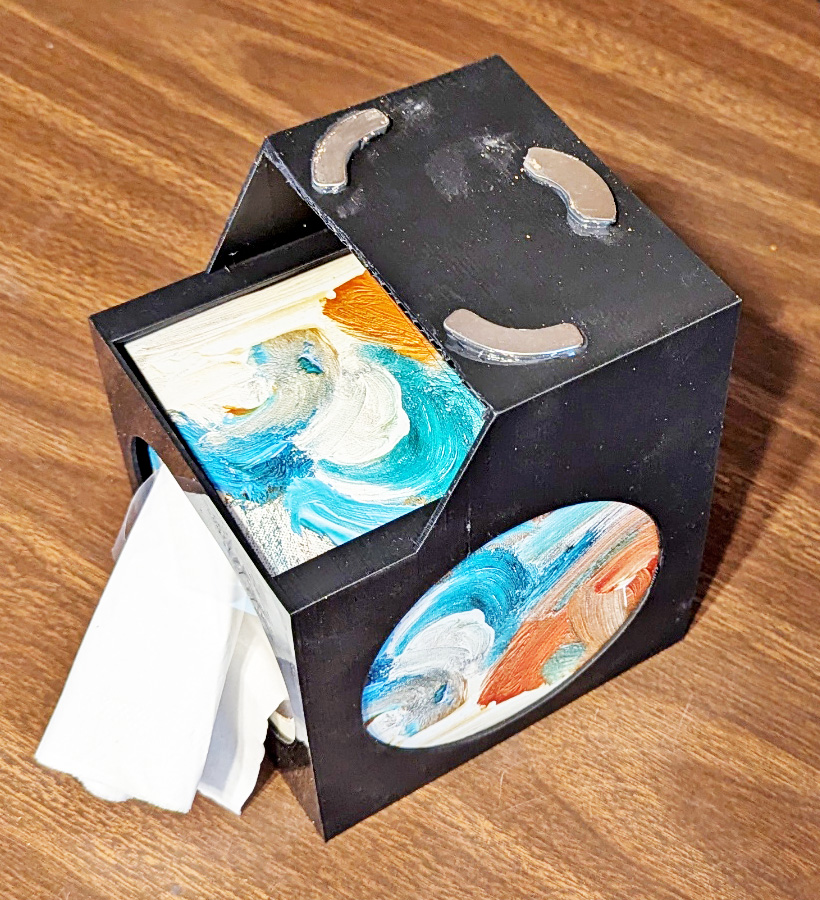
The boxes I designed could not be printed normally without having
fairly massive areas of support material. Anywhere there is
horizontal area of material in mid-air, supports
must be used or the molten filament will just fall. Angles of up
to 45 or 50 degrees from vertical work fine, but much past that and again the
material will either droop or fall.
By printing my cubes along an edge, all my angles are straight or 45
degrees and print just fine with the only support being a thin wall to
steady the cube on its edge.
The right shows the finished Kleenex box. The raised area goes up
to the bottom of the flat shelf to attach with magnets, while the front
is low enough to clear the flange at
the shelf edge and the outlet strip I have there. I use a tapered
construction shim to wedge the rear of the box in place to keep it from
being pressed out during use. If
that had not worked so well, I would have added a clip on the rear to hold the box in.
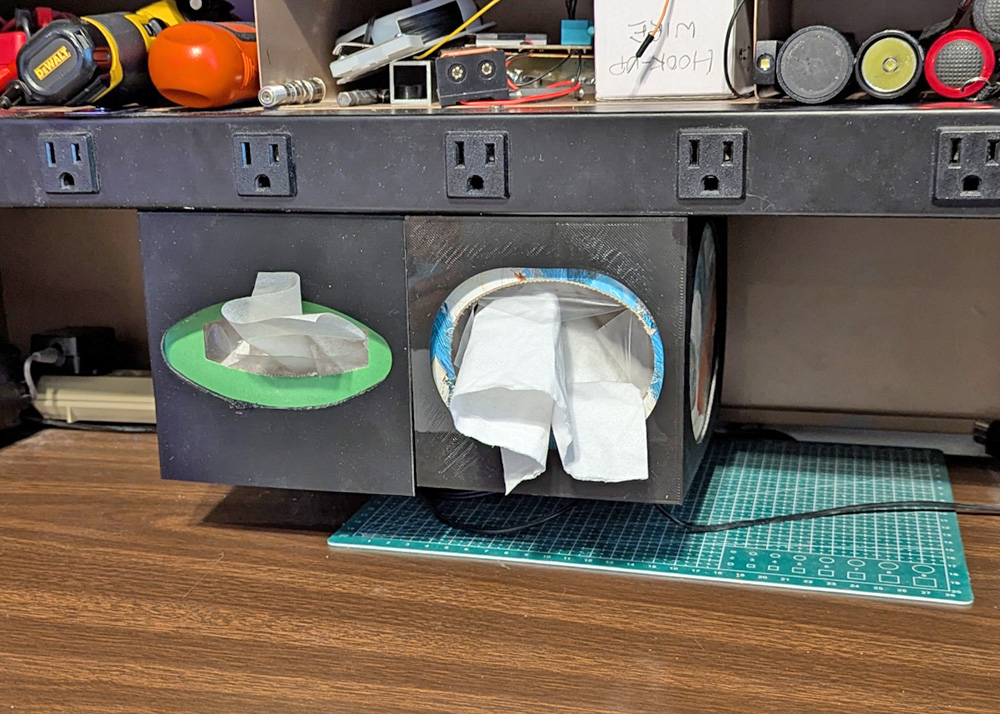
Mounted in place, the tissues can just be pulled when needed. The boxes leave
a space below for cables and flat items. They
are attached to the shelf above using magnets, so are easy to remove to replace the contents, or relocate along the shelf.
Deej Mixer
I recently saw an article on the Internet describing a multi-channel
audio mixer which plugs into your computer using a USB cable. It
can be built with the desired number of channels and those can be
assigned easily to any audio source. The project was named Deej,
probably pronounced DJ (but none of the YouTube presenters did).
Once I became aware of it, I found many videos and articles referencing
it, all with rave reviews and description of its excellent
operation. I decided to give it a try!
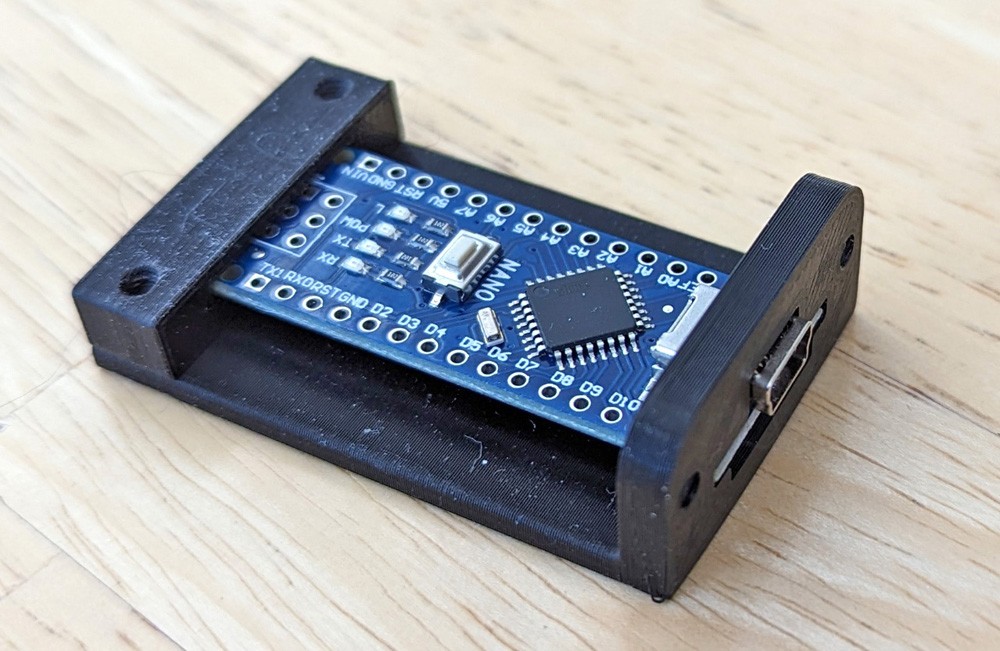
After a quick breadboard setup to prove it worked, I designed and
printed the basic case and the mount for the Arduino Micro
controller. I decided to make
a 5 channel mixer which gives me a spare channel or two.

Wiring was quite simple and much less than you would think. These views show the functionally completed unit.

I ran several trial runs for the label, and ended up with this one. It had the best legibility and quality,
with only a couple small spots where the white text did not quit fill in. I had to use white paint
to touch up these dots.
The performance is outstanding! The Master is identical to the main volume control using the tiny speaker icon
on the task bar. The Chrome knob controls the volume of any sound coming from my browser, think YouTube!
The best control of all is the Zoom knob. Zoom meetings always have been significantly louder than other audio,
and required me to click on the speaker icon, click on the pointer and drag it down. Then I had to repeat the
process and drag it back up when the Zoom meeting was done. I had tried doing this using the Windows mixer,
but it went away when the Zoom call was over, and came back the next time, again set far too loud. The Zoom
knob stays right where I left it and there is no more fiddling each time. I have not yet activated the remaining 2 knobs.
Webcam Mount
During the Covid pandemic, our computer society changed our normal
in-person meetings at the public library to remote Zoom meetings.
As things started to return to normal, we decided to try some "hybrid"
meetings, where we would have both in-person and remote Zoom
attendees. This was technically challenging! In working out
the details of how we would make all our proceedings equally accessible
to both local and remote members, the need for a webcam showing the
local members became apparent. Initially we mounted a
webcam on a camera tripod, which worked well, but was a hassle to
transport, set up, and take down.
The library recently installed a beautiful, new A/V setup comprising a
pair of large flatscreen TVs, webcams, and an integrated sound
system. This solved most of our earlier problems. We
attempted to use one of their webcams for our audience view, but
limitations to the system made it unavailable to the computer which
needed it. To avoid the tripod hassle, I designed a clamp-on,
fully adjustable mount for the camera which allowed attaching it under
one of the TVs.
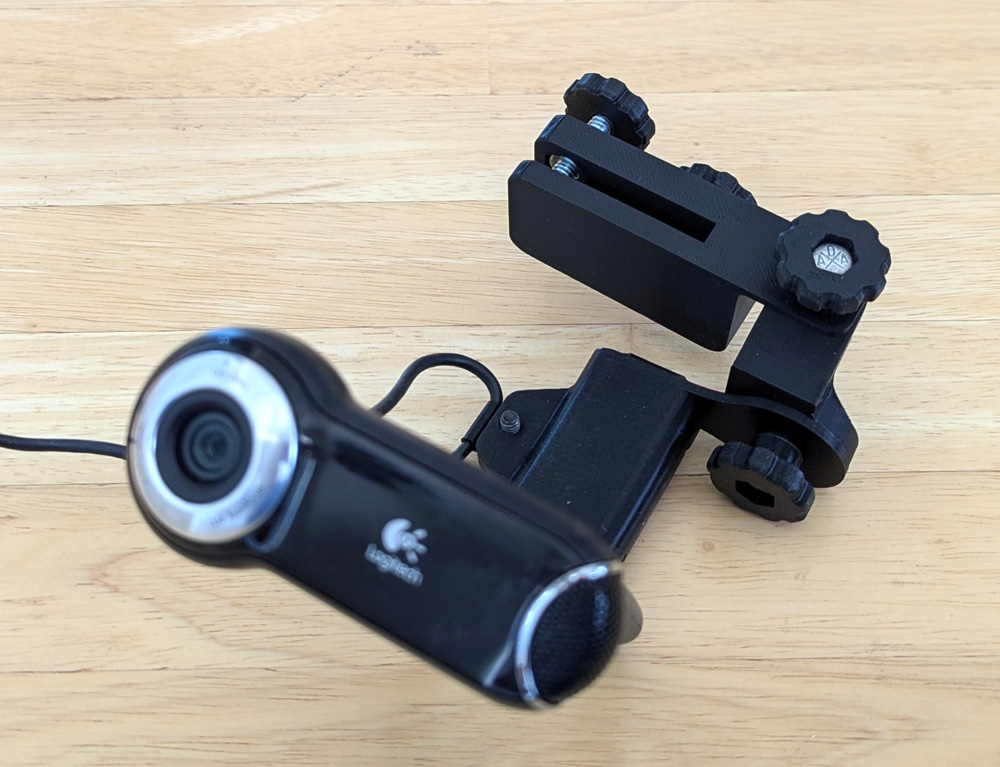
The left shows the library mounting of their webcam under the flat
screen TV. The mounting plate has a wonderful area for clamping
my camera!
The right shows the mount I made. The top portion clamps to the
aluminum angle, and the mount provides adjustments for leveling and
rotating the camera. The camera itself provides
for raising and lowering. This bracket makes setup much faster
than the tripod method, and will transport in my small parts bag.
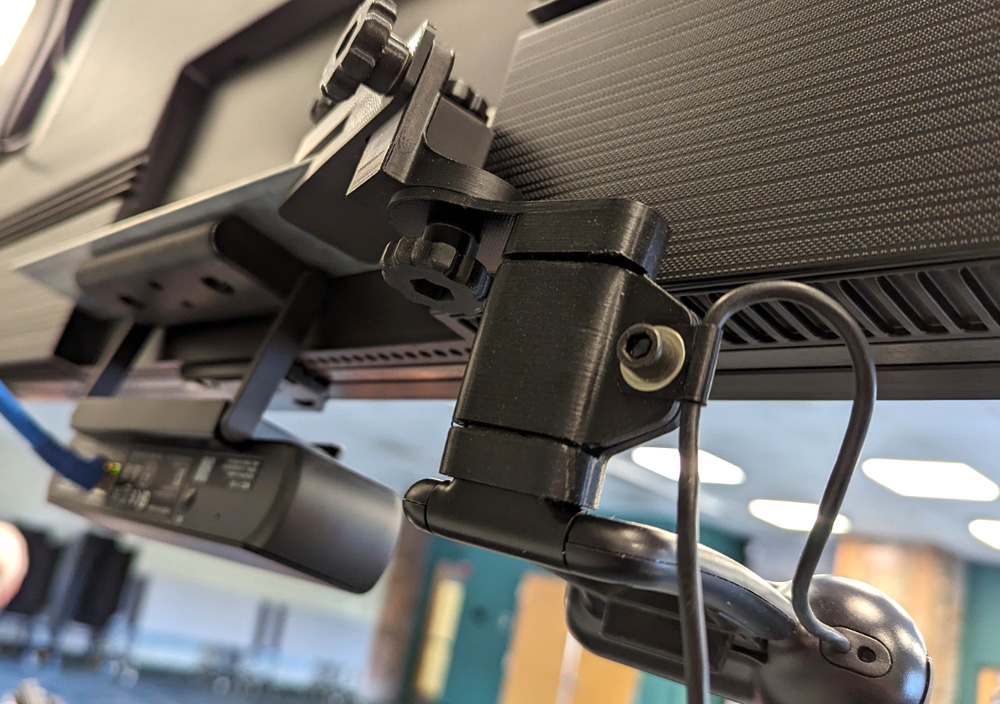
This shows the mounted camera from the rear. From the front, mostly all that shows is the camera.
Cable Holder
I have a spare monitor set up on the corner of my desk. I use
this monitor occasionally as a 3rd monitor for my computer or for
convenience when I am experimenting with some new electronics.
When not in use the AC power and the HDMI cords are just laid on the
desktop, where sometimes they slide down to the floor. It is
always a hassle to find the cords when I want to use this monitor.
After fighting with it recently, I decided to do a quickie fix and
solve the problem. Designing the part took about 5 minutes,
printing took about 38 minutes and boiling some water and bending the
tips up took maybe 10 minutes. From deciding to fix the problem
to a finished, installed part took about an hour. My cords are
now always off the floor and where I can immediately find them.
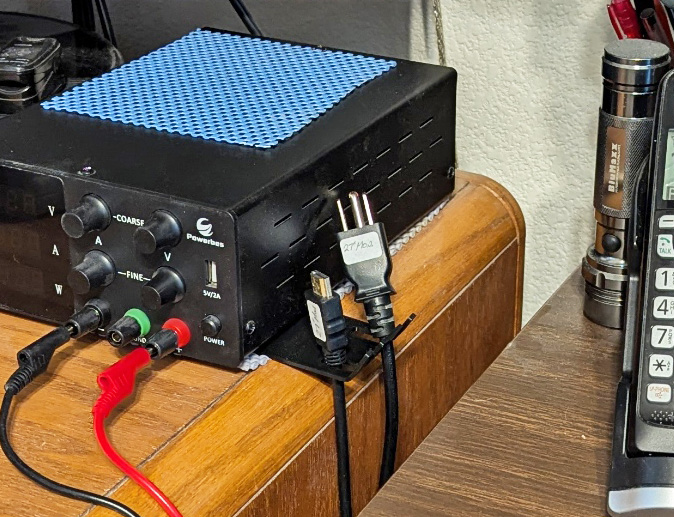
The cord holder was a very simple flat part, which I then heated to
bend the ends up to restrain the cords. I hold it in place with
the weight of the power supply I keep handy.
Water Heater Vent
I recently had a new water heater installed. In looking through
the manual it specified that an enclosed heater such as mine requires a
minimum of 100 square inches of ventilation to the outside area to
assure adequate burner combustion air. The existing vent was a
small metal plate with louvers in it. The total size of the
louvered area was less than 30 sq. inches.
I found a screen at Home Depot that was 8 x 16 inches, but it simply
had a flat metal edge. I designed and printed a frame to mount
and protect it. By splitting it in two, it still just barely fit my
printer, so I printed two halves and epoxied them together. I
used small steel pins to reinforce the joint. To cover the not
perfectly cut hole in the door, I printed two more pieces giving me an
inside frame, protection of the cut edges, and mounting bosses for the
outside screen's attachment.
The plumber also suggested changing the drain from under the house to
onto the garage floor, so any leak would be immediately seen. I
printed a small frame to surround this pipe also.
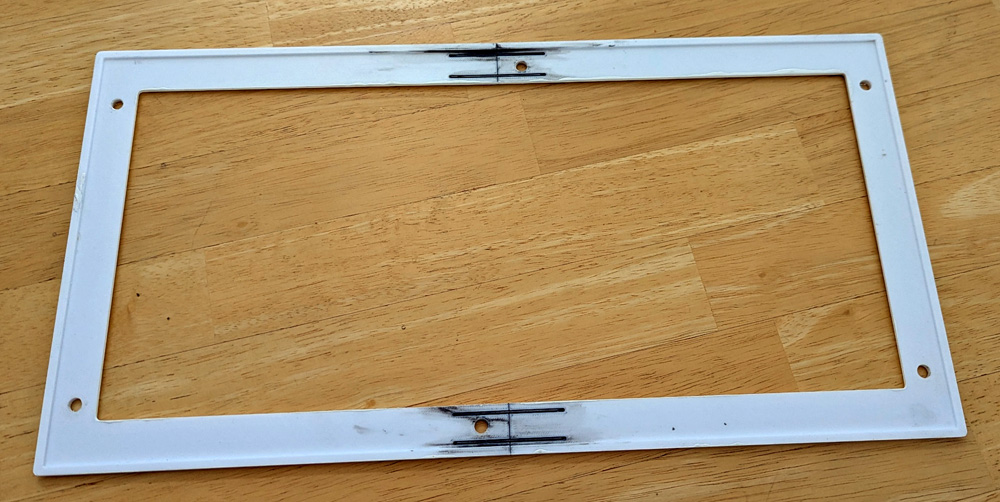
The pieces I printed along with the screen are on the left. I
have already epoxied the halves together and painted it in this shot.
The right shows the rear of the frame and the joints reinforced with the small pins.

The finished installation allows much more air to the burner, and includes the added drain pipe.
Mini-screwdriver Case
I recently bought a precision mini-screwdriver with inertially
controlled variable speed. It is the absolute top-of-the-line
according to the reviews, and I love it - except -- it did not include
a case! The best they did was the included cardboard box with a
pair of nice foam inserts to hold the tool and its 24 included bits.
In looking through a couple 3D printing sites I found a case
designed
specifically for this screwdriver set. It looked quite good, so I
printed it from his design files. It looks great and fits the
parts perfectly. There was just one problem: The hinge
setup was very wonky. The designer used links hinged to both the base and the lid. This means the the lid
has no restraints when open and just flops and twists around. Of
course it would work, but I want a "proper" hinge! If I had the
true CAD file for this, redesigning the hinge would be easy, but as
with most of these download-and-print items, only the printer file is
provided, which is difficult to edit more than simple changes. I designed a part to replace his double-hinge-link,
which fits the outline of the case exactly on the bottom end. The
screw holds the shaped bottom tightly against the outside of the case,
keeping it rigid. The top hole becomes
the only hinge point, and is slotted slightly to allow proper alignment
as you
close it. I am now pleased as the lid is restrained when
open.
The tool came with this box and the foam inserts. I had already moved the bits to the new case when
I took this picture, so there is only 1 bit in the foam, but it came full of bits.

The end view of the case shows the two hinge points which originally
used the black link on the right. The rigid link I designed
is in orange on the right
and is shown installed in the left picture. Only the top screw is a hinge point now.
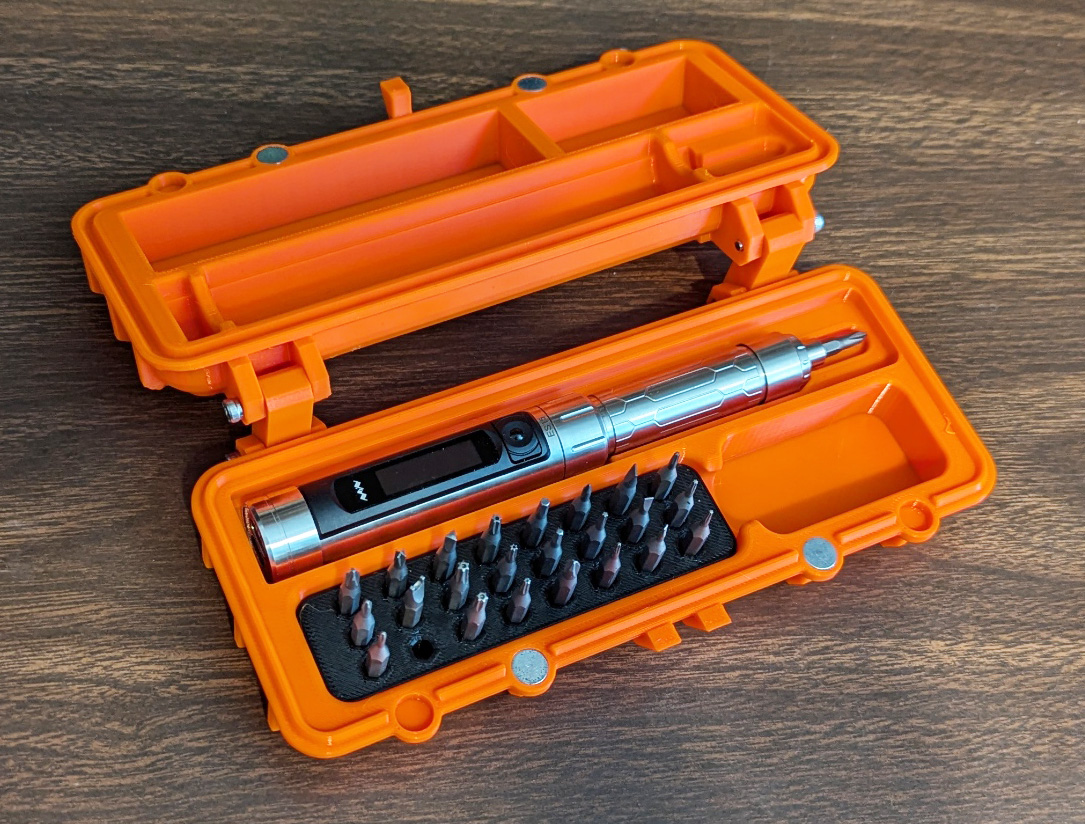
The case is an attractive, functional case which fits the screwdriver
and its bits perfectly. There are magnets to hold it
closed. With its modified
hinge system, I am totally happy with it!
Many thanks to zx82net who designed the Ultimate Parametric Rugged Box
and to 3DP-MAMSIH who adapted that to fit the ES15 screwdriver!
CPAP Hanger
I need to use a CPAP machine at night. Along with its normal list
of annoyances, during the day there really is no good place to put the
hose and mask. I have been just stretching it across the head of
the bed. A couple nights ago (as I write this) I decided to make
a proper hanger for it. I rather quickly designed a simple hook
that slips over a board on my headboard and provides a generous hook
for hanging my hose and mask.

And here is the hook and it in use holding my mask and hose.
Component Tester Case
Several years ago, I bought a small universal component tester for
about $7 after reading great reviews. When it did not arrive in a
fairly long time, the vendor sent me a second one. About a month
later the original one arrived! The vendor said to keep
both. The original unit was described as coming with a Plexiglas
case and a back light in the display. The replacement
one was just a board with an attached battery holder, and the unit did
not have a backlit display. I keep the "good" one in my shop
and the bare board version in my office.
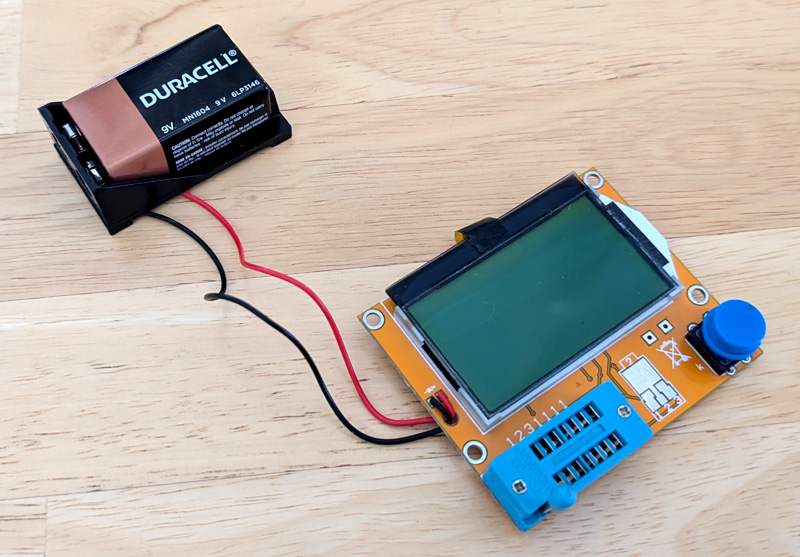
The replacement unit works fine, but is quite awkward with the
attached battery and no protection.
I decided to make a case for it. I measured the board and
battery case accurately and drew 3D representations of them in my CAD
program, then I drew the case parts around them. I was pleased
that once I printed the top and bottom halves of the case they fit
perfectly and I only discovered one small error, which was easily
corrected, (See picture description below).
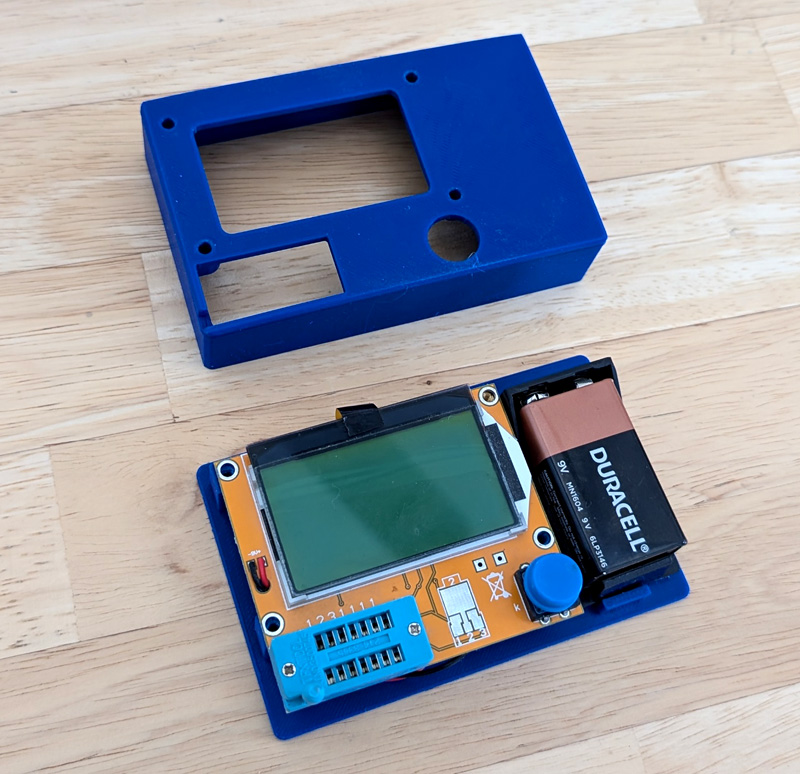
The two case halves sandwich the board and battery, and clamp the board securely between the mounting posts on both halves.
The one error I found was on one of the base mounting posts. As I
used a single sketch to build both halves, the holes in the posts
were shown as two concentric circles, the larger one to clear the
screws in the top, and the smaller ones to thread in the screws to
the bottom post. On one of the base posts, I accidentally
selected the inner circle instead of the ring between them. The
result was an
oversize hole with a post in the center. I drilled out the post,
and sized the top end for a heat installed insert. Now I have
brass threads
in that hole and the problem is solved.

And here is the finished case.
Cluttered Cord Manager
When I built my present main desktop computer, I moved my old one to my side desk for use as a secondary
system. I have done this for several iterations in the past.
I wanted the flexibility of being able to easily change peripherals of
this computer and being able to use the keyboard, mouse, and monitor
with other systems for testing and repair. To this end I made
sure all the cables coming up from the computer under the desk had a
termination on the desk. This made it handy to connect most
anything the way I wanted for the moment, but left a major clutter of
cables. The terminations consisted of extension cables which
ended on the surface of my desk. From there, all the peripherals
plugged into those loose cables.
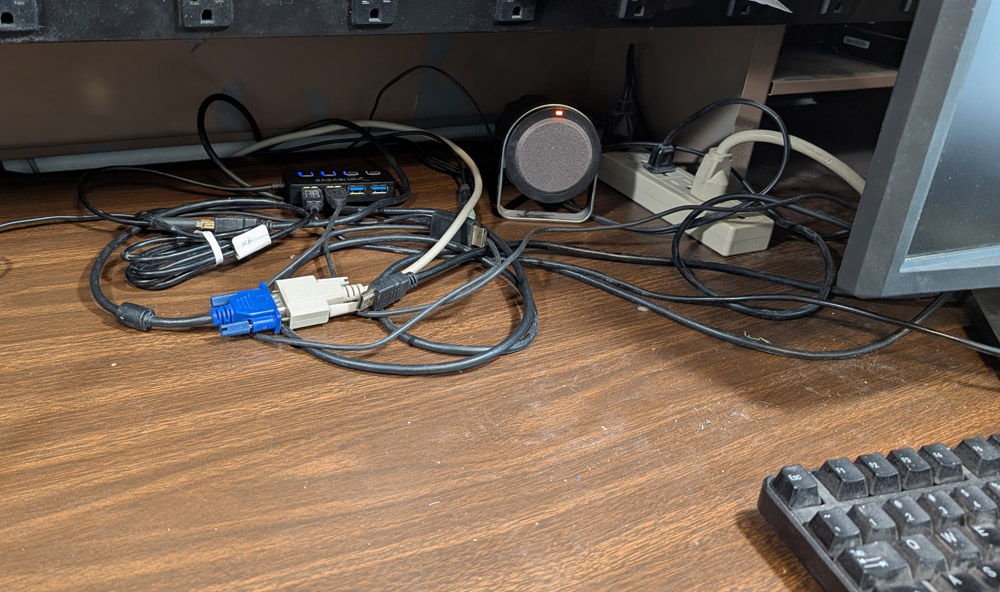
This
is the clutter on my side desk, and this is highly sanitized, after
removing 2 power cables and one USB cord that were never removed after
testing
other devices, and were tangled into a non-decipherable mass! It
was just a large pile of assorted, hard to identify cables.
My initial thoughts were to make a tray of some kind which
would hold the coiled up cables and attach it under the bottom shelf of
the hutch. As I was figuring how to do this, things got much more
complex! Funny how that works! Instead of just a tray, I
wanted to mount all the connectors of cables coming up from the
computer. These included a VGA output, an HDMI cable, a single
USB 3.0 connection, and the speaker jack.
I then started designing my tray with openings and clamping blocks for
each connector along with a provision to attach a USB hub to the
bottom. As done with several previous projects, I wanted to mount
it to the steel shelf with magnets. Over the years I have
scrapped many defunct hard drives, which all contain very powerful
neodymium magnets and I have a pretty good collection of them by now.
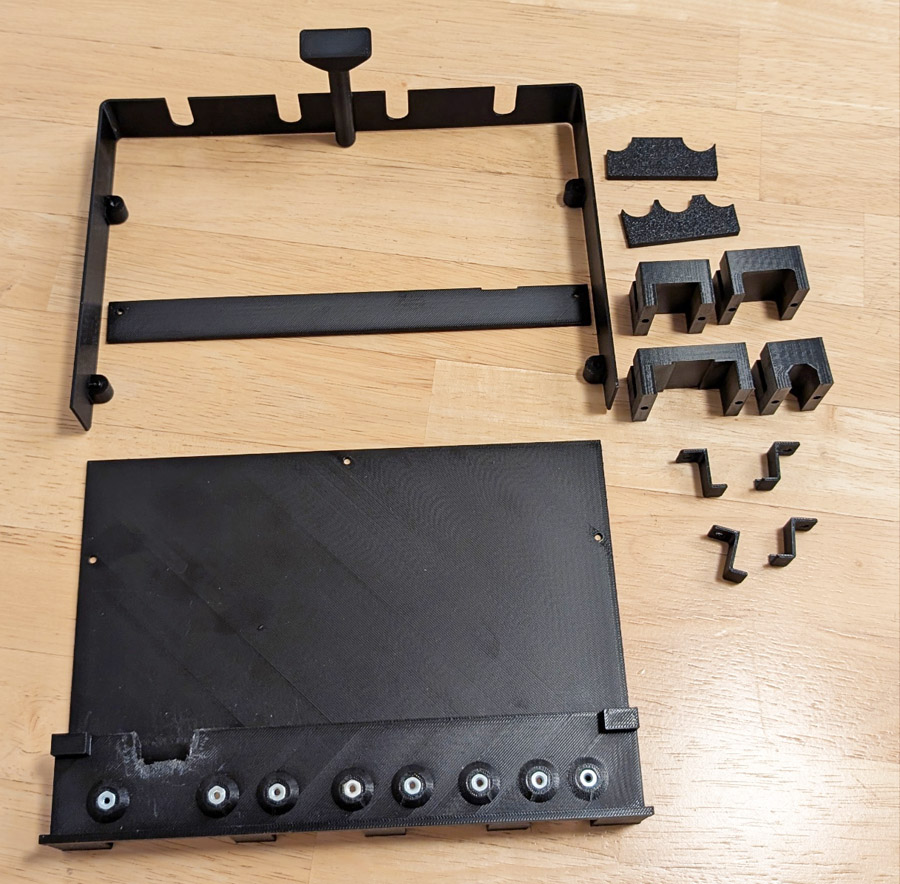
I ended up with more printed parts than I had expected, but here they are. The flat strip near the top mounts
on the two tabs of the main frame and provides support for the vertically mounted magnets. The
two scalloped pieces are spacers which mount the horizontal magnets at the correct height. The 4 blocks
are each tailored to closely fit the cables I need to mount and securely clamp them in place. The 4 "Z" clips
mount the USB hub.
This picture also shows the "cutout of shame". A groove to fit the VGA plug did not continue all across the top
mount piece, and with the narrow gap around it would have been very hard to correct, so I just cut that section
out. The easiest way was to use a hot-knife tip on my soldering iron. It made a real mess of melted plastic
around the cut which took far longer to clean up than the cut took. I really am not worried about the looks
as it is totally hidden by one of the magnet blocks, and that is totally hidden after installation.
This view also shows the pressed-in nuts used to screw in the cable clamping blocks and the 4 mounting
tabs for the USB hub (not shown). Hexagon shaped pockets are printed, then nuts are pressed in. This makes
for a secure metal to metal connection where screws are expected to be inserted and removed several times
during an items lifetime. Heat set inserts would also have worked well here, but all of mine are metric and
I am using 4-40 screws in this project.
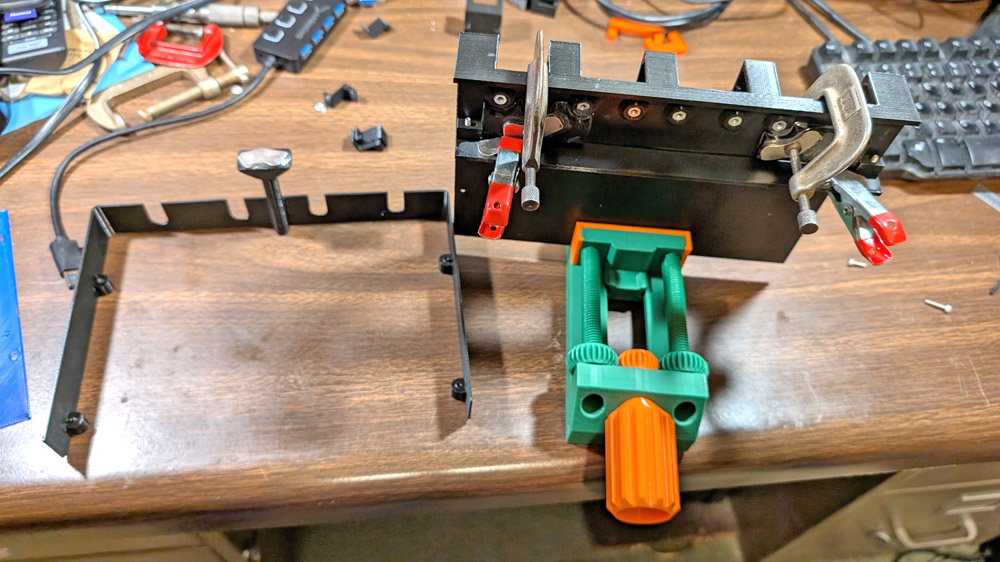
The messiest part of this project was epoxying the magnets in place. The main frame is being held
by a vise I 3D printed.

And here is the unit fully assembled except for the cables. The
four magnets in the foreground attach to the electrical receptacle bar
along the
front of the shelf, which is itself attached with magnets. The
magnet on the post in the rear attaches to the bottom of the shelf and
merely
stabilizes the rear of the unit.
On the right, the USB hub is secured using 4 small clips.
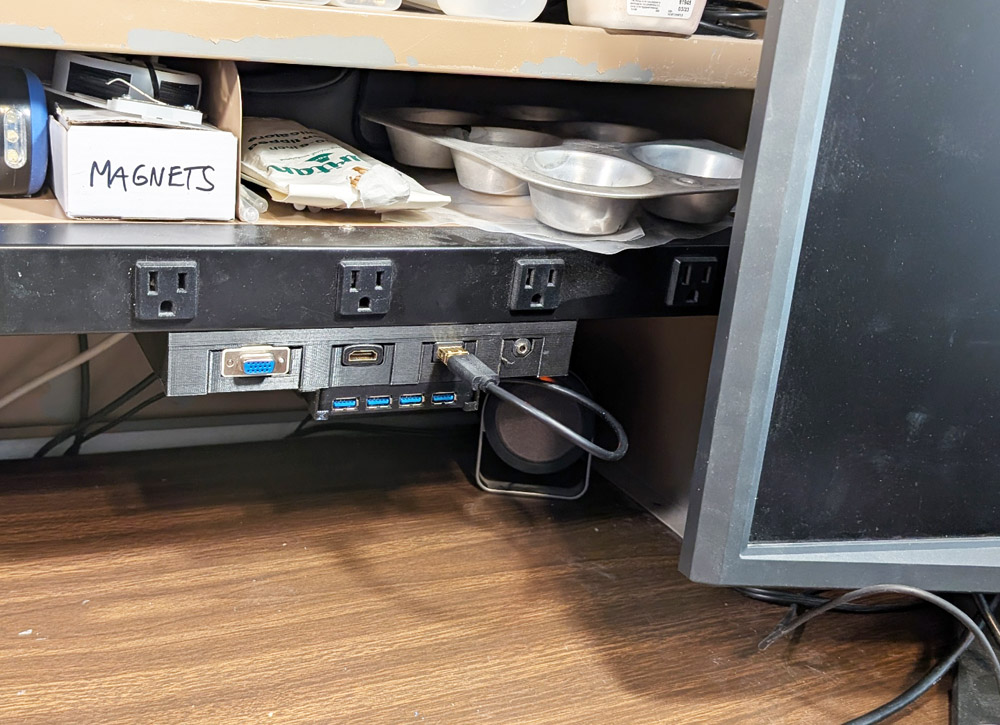
The system is now installed, and all the cables are readily accessible. I must have done my math correctly
as it is positioned just as I intended.
There was a power strip in this area also, adding to the clutter. I jacked up the end of the hutch (it is very
heavy) enough to slide the power cable under the hutch divider, into the right hand section. Here is is totally
out of the way, and practically invisible.

And here is my final setup, with everything connected and working. Now, not only is my desk much less cluttered, but also
it is easy to disconnect and re-configure everything as needed for testing peripherals or whole systems.