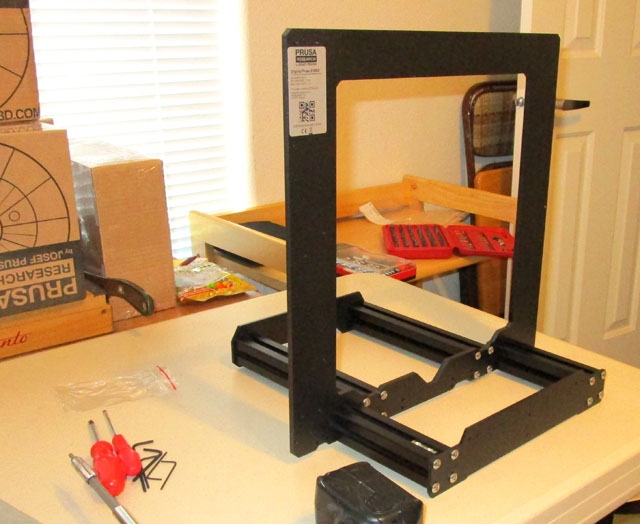
Assembly started by assembling the basic framework. This frame
holds all the components of the printer
and must be very square and rigid.
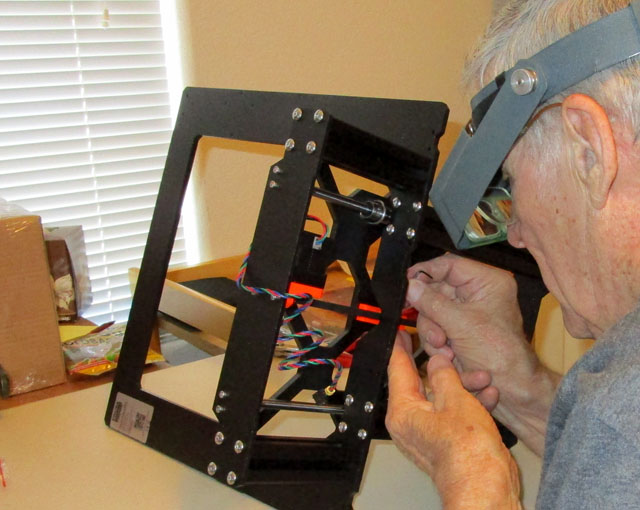
On the left I am assembling the linear ball bearings for the Y axis and
the precision
rods they ride on. They must also be aligned precisely. The
manual details
how to do this easily. On the right I am installing and adjusting
the lug belt which positions the table along the Y axis.
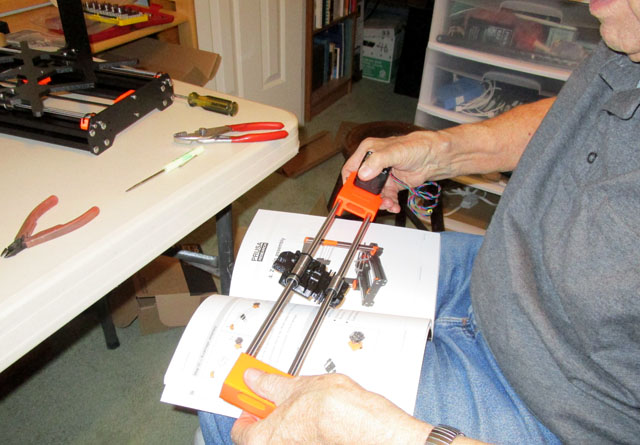
The X axis assembly is one of the simplest. A carriage rides on
precision rods with linear ball bearings. A stepper
motor at one end drives a lug belt to position the carriage.
Next, this completed X assembly is mounted on a pair of vertical rods
and two stepper motors and leadscrews forming the Z axis. All the
positioning components are now
complete. The table moves the work in and out for the Y axis
movement. The carriage moves left and right to position the
extruder correctly in the X axis, and
that whole assembly moves up and down to the correct Z height.

Now the extruder assembly is built up and installed on the
carriage. There are many, many wires coming from
this assembly. These include heater power, heat sensor, extruder
stepper motor, filament sensor, sensor to
set exact height above the table, and power to the two fans.
There is also a nylon rod which will be bundled
with the wires to maintain the shape of the bundle as it moves.
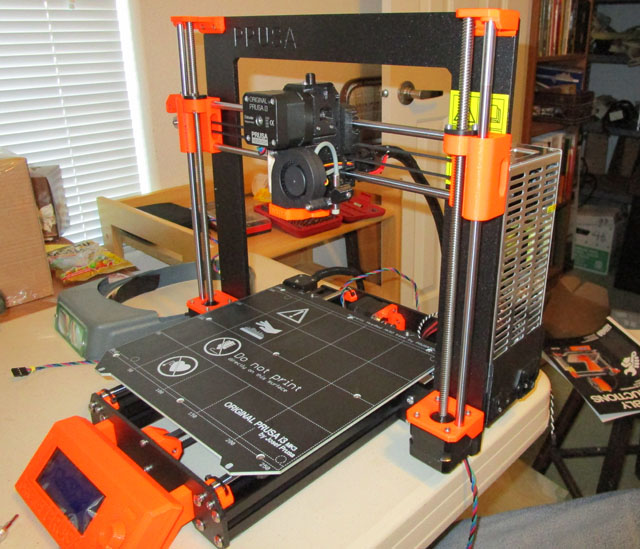
Here we see all the wires from the last photo are now gathered into a
neat bundle and covered with spiral
wrap. Also the heated table has been installed. This plate,
in addition to housing the heater contains 20 very
powerful, high temperature magnets which hold the treated steel build
plate securely in place, yet making
it easy to remove.

Prusa is very particular about wire management. They tell you
exactly where to run each wire, where to place every zip tie, and often
even which way
the zip tie is placed and where the head should wind up. On the
right we see the wiring to the computerized controller, the Einsy
board, named after Albert
Einstein because it is so smart. Pretty much every wire on
the machine ends up attaching to this board.

We have finished the assembly of all parts of the machine. Now we
have it fired up and are running the
automatic calibration routines. Among other things, these routines
exactly measure any out-of-square conditions
and keep a correction table to make sure the parts come out exactly
right.
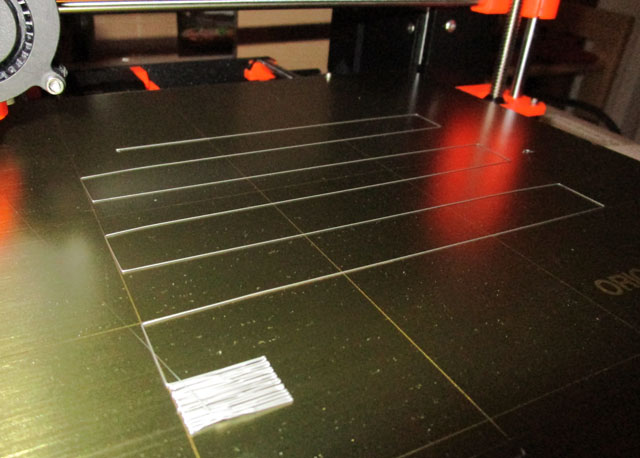
The first layer of plastic deposited is the most critical portion of
the entire printing cycle. The height of the nozzle
over the table must be set very accurately, and cannot be done
automatically. This is a test pattern to assist in
setting this height. As we see it here, we are still a long way
from having it correct. When it is correct, you
can see that the zig zag lines are squashed to about half thickness,
and the square at the bottom is smooth
and flat, with no voids or bumps.
After completing this step, we were ready to start making things!